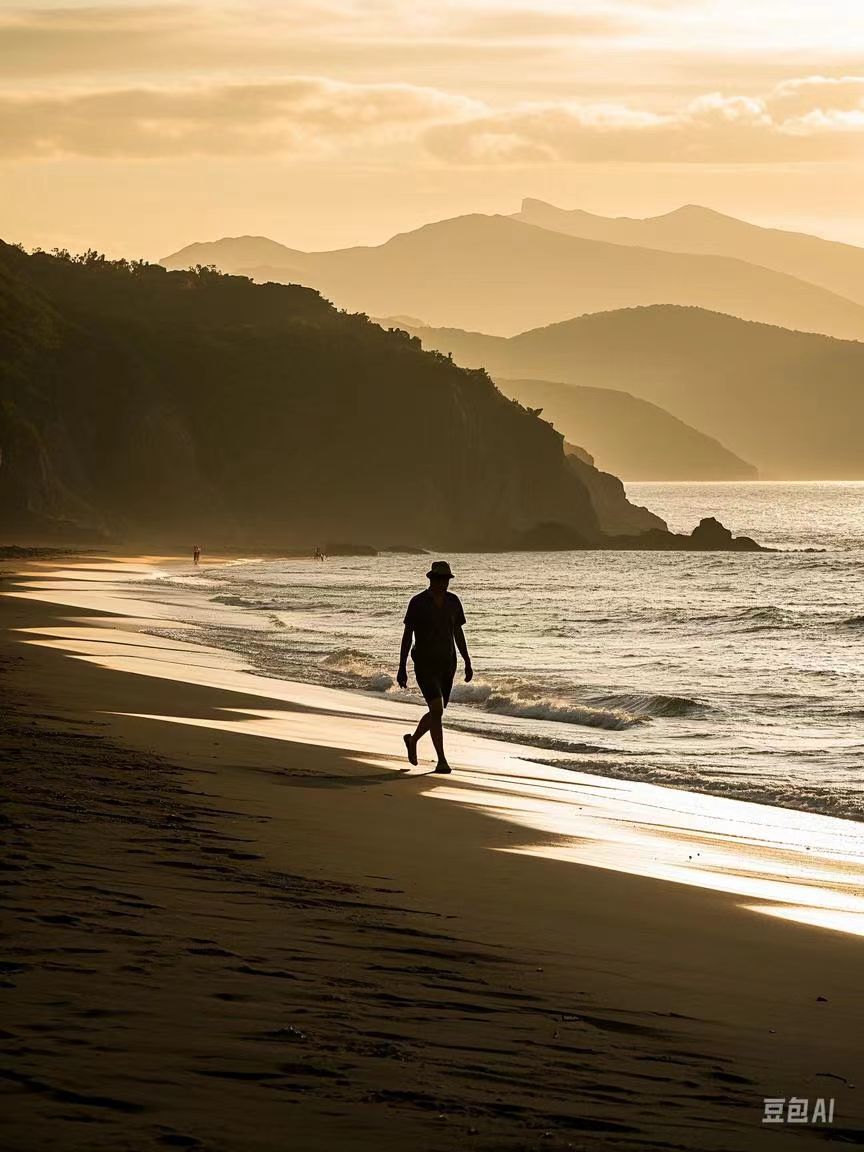
About Oxygen Concentrator
An oxygen concentrator
Technical field
The utility model relates to an oxygen concentrator, which belongs to the field of medical devices.
Background technology
The oxygen concentrator we often talk about is expressed in English as "Oxygen concentrator", which means oxygen collector. According to the principle, there are two common oxygen collectors on the market: one is to produce oxygen with molecular sieves, and the other is to produce oxygen with "oxygen-attached membrane" also known as "oxygen-enriched membrane". The first "molecular sieve" PSA oxygen concentrator was first manufactured by the German company Delin, which is almost 100 years ago. In the 1970s, small molecular sieve oxygen concentrators in the United States began to enter the field of home oxygen therapy. The working principle of household oxygen concentrators and most medical oxygen concentrators is to separate oxygen and nitrogen based on the difference in the adsorption capacity of the attractant (zeolite molecular sieve) for oxygen and nitrogen in the air. When air enters the bed containing adsorbent, nitrogen has a strong adsorption capacity and is adsorbed, while oxygen is not adsorbed, so that a high concentration of oxygen can be obtained at the outlet of the adsorption bed. Since the adsorbent has the characteristic that its adsorption amount changes with pressure, changing its pressure can make the adsorption alternate between adsorption and desorption operations. However, the current oxygen generator has poor air filtration effect, which directly affects the life of the compressor and molecular sieve, because the particulate impurities in the air enter the cylinder, which will cause the cylinder leather cup to be damaged, affecting the air tightness of the cylinder, thereby reducing the oxygen production efficiency. The air contains moisture, and if no measures are taken to allow it to enter the molecular sieve tower, it will seriously affect the service life of the molecular sieve.
Utility model content
The technical problem to be solved by the utility model is to provide a safe and reliable oxygen generator that enhances the air filtration effect and increases the service life of the compressor and molecular sieve adsorption tower.
In order to solve the above technical problems, the technical solution adopted by the utility model is:
An oxygen generator, characterized in that: an adsorption drying device is provided at the air outlet of the air filter, an air intake silencer is provided at the air outlet end of the adsorption drying device, an oil-free air compressor is provided at the air outlet end of the air intake silencer, the air outlet of the oil-free air compressor is connected to the molecular brush adsorption tower, the air outlet of the molecular brush adsorption tower is arranged with an oxygen storage tank, the air outlet of the oxygen storage tank is connected to the purification oxygen supply system, and the air outlet of the purification oxygen supply system is connected to the oxygen flow meter and the oxygen outlet.
Further, in the oxygen concentrator, a back pressure valve is arranged between the gas outlet of the oxygen storage tank and the purified oxygen supply system, and the gas outlet of the molecular sieve adsorption tower is connected to the gas inlet of the oxygen storage tank through a one-way valve.
Further, in the oxygen concentrator, two containers are arranged in the adsorption drying device, one of which is filled with a coarse dehydration adsorbent, and the other is filled with a deep dehydration adsorbent.
The working principle of the oxygen concentrator of the utility model is: after the air enters the air filter, the impurities such as moisture and dust in the air are filtered out, and then the air is further dehydrated by the adsorption drying device, and the air comes out of the adsorption drying device and enters the air intake silencer for noise reduction. The gas after noise reduction is compressed by an oil-free air compressor, and the compressed air enters the molecular brush adsorption tower to adsorb nitrogen, thereby maintaining a high concentration of oxygen, and then the oxygen is collected in the oxygen storage tank, and a back pressure valve is arranged between the gas outlet of the oxygen storage tank and the purified oxygen supply system, which increases the effect of removing carbon dioxide while stabilizing the pressure of the gas. After that, the purified oxygen supply system further adjusts the purity of the oxygen. When the outlet of the purified oxygen supply system is connected to an oxygen flow meter, its high-purity oxygen output flow rate is controlled, and finally, the high-purity oxygen is output to the patient through the oxygen outlet.
The oxygen concentrator provided by the utility model is reasonably designed, safe and reliable, enhances the air filtration effect, and increases the service life of the compressor and the molecular sieve adsorption tower, and is suitable for universal promotion and application.
Description of the drawings
Figure 1 is a structural schematic diagram of the utility model.
Specific implementation methods
The utility model is further described below in conjunction with the drawings.
As shown in Figure 1, an oxygen concentrator is characterized in that: an adsorption drying device is provided at the outlet of the air filter, an air intake silencer is provided at the outlet end of the adsorption drying device, an oil-free air compressor is provided at the outlet end of the air intake silencer, the outlet of the oil-free air compressor is connected to a molecular brush adsorption tower, the outlet of the molecular brush adsorption tower is arranged with an oxygen storage tank, the outlet of the oxygen storage tank is connected to the purified oxygen supply system, and the outlet of the purified oxygen supply system is connected to the oxygen flow meter and the oxygen outlet.
Furthermore, in the oxygen concentrator, a back pressure valve is provided between the gas outlet of the oxygen storage tank and the purified oxygen supply system, and the gas outlet of the molecular sieve adsorption tower is connected to the gas inlet of the oxygen storage tank through a one-way valve.
Further, in the oxygen concentrator, two containers are provided in the adsorption drying device, one of which is provided with a coarse dehydration adsorbent, and the other is provided with a deep dehydration adsorbent.
When the oxygen concentrator is used, after the air enters the air filter, the impurities such as moisture and dust in the air are filtered out, and then the air is further dehydrated by the adsorption drying device, and the air comes out of the adsorption drying device and enters the air intake silencer for noise reduction. The gas after noise reduction is compressed by an oil-free air compressor, and the compressed air enters the molecular brush adsorption tower to adsorb nitrogen, thereby maintaining a high concentration of oxygen, and then the oxygen is collected in the oxygen storage tank, and a back pressure valve is provided between the gas outlet of the oxygen storage tank and the purified oxygen supply system, which increases the effect of removing carbon dioxide while stabilizing the pressure of the gas. After that, the purified oxygen supply system further adjusts the purity of the oxygen. When the outlet of the purified oxygen supply system is connected to an oxygen flow meter, the high-purity oxygen output flow rate is controlled, and finally, the high-purity oxygen is output to the patient through the oxygen outlet.
The adsorption drying device equipped with a coarse dehydration adsorbent and a deep dehydration adsorbent can achieve deep dehydration and impurity removal of gas.
A back pressure valve is arranged between the outlet of the oxygen storage tank and the purified oxygen supply system, which stabilizes the gas pressure while increasing the function of removing carbon dioxide.
The above is only a preferred embodiment of the utility model. It should be pointed out that for ordinary technicians in this technical field, several improvements and modifications can be made without departing from the principle of the utility model, and these improvements and modifications should also be regarded as the protection scope of the utility model.